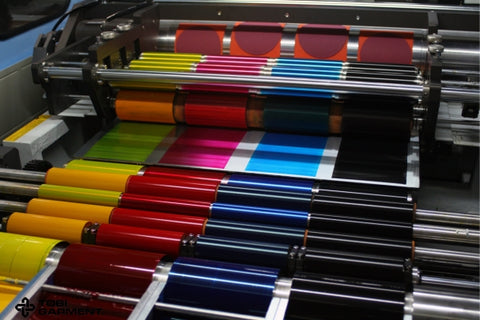
Water-based screen printing is an exciting and eco-friendly method of printing that has gained immense popularity in recent years. As someone who has delved into the world of screen printing, I can attest to the joy and satisfaction that comes from creating vibrant, high-quality prints while minimizing environmental impact. This guide will explore the ins and outs of water-based screen printing, providing you with detailed instructions, practical tips, and insights into its benefits and applications.
What is Water-Based Screen Printing?
Water-based screen printing is a technique that utilizes water-based inks to create designs on various substrates, primarily fabrics. Unlike traditional plastisol inks, which contain harmful chemicals and require solvents for cleanup, water-based inks are made from natural pigments and water, making them a safer and more sustainable option.
Water-based inks penetrate the fabric fibers, resulting in a soft, breathable print that feels comfortable against the skin. This method is particularly popular for printing on apparel, home textiles, and promotional products.
How Does It Differ from Solvent-Based Screen Printing?
The primary difference between water-based and solvent-based screen printing lies in the composition of the inks. Here’s a brief comparison:
Feature |
Water-Based Screen Printing |
Solvent-Based Screen Printing |
Ink Composition |
Natural pigments and water |
Chemicals and solvents |
Environmental Impact |
Eco-friendly, low VOC emissions |
Higher VOC emissions, less eco-friendly |
Print Feel |
Soft, breathable |
Thick, plastic-like finish |
Cleanup |
Water-based, easy cleanup |
Requires solvents for cleanup |
Curing Process |
Air-dried or heat-cured |
Heat-cured, often requires higher temperatures |
This comparison highlights the advantages of water-based inks, particularly in terms of environmental sustainability and print quality.
Read more: Elevate Your Style with Custom Screen Print Shirts
What Are the Benefits of Using Water-Based Inks?
Using water-based inks offers numerous benefits that make them an attractive choice for screen printers:
- Eco-Friendly: Water-based inks are less harmful to the environment, producing fewer VOCs and reducing pollution.
- Comfortable Prints: The ink penetrates the fabric, resulting in a soft feel that is comfortable to wear.
- Vibrant Colors: Water-based inks can produce bright, vivid colors that stand out beautifully on fabrics.
- Versatility: These inks can be used on a variety of substrates, including cotton, polyester, and blends.
- Easy Cleanup: Since the inks are water-soluble, cleanup is straightforward, requiring only water and soap.
The Water-Based Screen Printing Process
Embarking on a water-based screen printing project can be a fulfilling experience. Here’s a step-by-step guide to help you navigate the process effectively.
Preparing the Substrate
- Choose Your Fabric: Select a fabric suitable for water-based printing. Cotton and cotton blends work exceptionally well.
- Pre-Wash the Fabric: Wash the fabric to remove any finishes or residues that may interfere with ink adhesion. Allow it to dry completely.
- Set Up Your Workspace: Ensure your workspace is clean and organized. Gather all necessary materials, including screens, squeegees, and inks.
Creating the Stencil
- Design Your Artwork: Create your design using graphic design software. Ensure it is suitable for screen printing.
- Print the Design on Film: Print your design onto transparent film. This will serve as your stencil.
- Prepare the Screen: Coat your screen with emulsion evenly and allow it to dry in a dark environment.
- Expose the Screen: Place the film on the screen and expose it to UV light according to the emulsion manufacturer’s instructions. This will harden the emulsion where the design is not present.
- Wash Out the Screen: Rinse the screen with water to remove the unexposed emulsion, leaving behind your stencil.
Applying the Ink
- Set Up the Screen: Secure the screen on the printing press or a flat surface.
- Position the Fabric: Lay your fabric flat beneath the screen, ensuring it is aligned correctly.
- Pour the Ink: Pour a line of water-based ink along the top of the screen.
- Use the Squeegee: With a squeegee, pull the ink across the screen in a smooth motion, ensuring even coverage.
- Lift the Screen: Carefully lift the screen to reveal your printed design.
Curing the Print
- Air Dry: Allow the print to air dry for a few minutes.
- Heat Cure: Use a heat press or conveyor dryer to cure the print. Follow the ink manufacturer’s instructions for temperature and time.
- Test the Print: After curing, test the print for durability by washing it. Ensure it holds up well without fading or cracking.
Read more: Eco-Friendly Screen Printing: Your Guide to Sustainable Style
Water-Based Ink Types
Understanding the different types of water-based inks available will help you select the right one for your project.
Pigmented Inks
Pigmented inks use pigments suspended in a water-based solution. They provide excellent color vibrancy and opacity, making them ideal for printing on dark fabrics.
Dispersed Inks
Dispersed inks are specifically designed for synthetic fabrics, such as polyester. They are often used in dye-sublimation printing, allowing for vibrant, long-lasting prints.
Reactive Inks
Reactive inks chemically bond with the fabric fibers, providing excellent wash fastness and color vibrancy. They are particularly effective for cotton and other natural fibers.
Read more: A Step-by-Step Guide to Screen Printing on Wood
Common Applications of Water-Based Screen Printing
Water-based screen printing is versatile and can be applied to various products. Here are some common applications:
Apparel
Water-based screen printing is widely used for t-shirts, hoodies, and other clothing items. The soft feel of the prints makes them comfortable for everyday wear.
Home Textiles
From pillowcases to curtains, water-based inks can be used to create beautiful designs on home textiles, adding a personal touch to any space.
Promotional Products
Businesses often use water-based screen printing for promotional items like tote bags, hats, and banners. The eco-friendly nature of the inks appeals to environmentally-conscious consumers.
Industrial Applications
Water-based inks are also used in industrial applications, such as printing on packaging materials and labels, where sustainability is a key consideration.
Choosing the Right Water-Based Ink
Selecting the appropriate water-based ink for your project is crucial for achieving the desired results. Here are some factors to consider:
Considering Fabric Type
Different fabrics react differently to various inks. Always choose an ink that is compatible with your substrate for the best results.
Assessing Design Complexity
For intricate designs, consider using inks that offer better opacity and detail retention. Pigmented inks are often a good choice for complex artwork.
Evaluating Environmental Requirements
If sustainability is a priority, opt for inks that are certified eco-friendly and low in VOC emissions.
Balancing Cost and Performance
While it may be tempting to choose the cheapest option, consider the long-term performance and durability of the ink. Investing in high-quality inks can save you money in the long run.
Read more: The Ultimate Guide to Screen Printing T-Shirts
Tips for Successful Water-Based Screen Printing
To ensure a successful water-based screen printing experience, keep these tips in mind:
Maintaining Proper Ink Viscosity
Water-based inks can thicken over time. Use a viscosity cup to check and adjust the ink’s thickness as needed for optimal printing.
Ensuring Accurate Stencil Alignment
Take the time to align your stencil properly. Misalignment can lead to distorted prints and wasted materials.
Optimizing Curing Conditions
Follow the manufacturer’s recommendations for curing temperatures and times to ensure the longevity of your prints.
Troubleshooting Common Issues
Be prepared to troubleshoot common issues, such as ink bleeding or fading. Regularly clean your screens and squeegees to maintain print quality.
Environmental Benefits of Water-Based Screen Printing
Water-based screen printing is not only beneficial for the printer but also for the environment. Here are some key environmental advantages:
Reduced VOC Emissions
Water-based inks produce significantly lower levels of volatile organic compounds (VOCs) compared to solvent-based inks, contributing to better air quality.
Improved Air Quality
By using eco-friendly inks, you help create a healthier workspace and contribute to a cleaner environment.
Compliance with Environmental Regulations
Many industries are moving towards sustainable practices to comply with environmental regulations. Water-based screen printing aligns with these efforts.
Contribution to Sustainability
Choosing water-based inks supports sustainable practices and reflects a commitment to protecting our planet for future generations.
Conclusion
Water-based screen printing is a vibrant and eco-friendly method that allows for creativity while promoting sustainability. By understanding the process, types of inks, and applications, you can harness the power of water-based printing to create stunning designs that resonate with consumers.
FAQ
1. What is water-based screen printing?
Water-based screen printing is a printing technique that uses water-based inks to create designs on various substrates, primarily fabrics.
2. How do water-based inks differ from solvent-based inks?
Water-based inks are made from natural pigments and water, making them eco-friendly and soft on fabrics, while solvent-based inks contain chemicals and solvents that can be harmful to the environment.
3. Can I use water-based inks on synthetic fabrics?
Yes, but it is essential to choose the right type of water-based ink, such as dispersed inks, which are specifically designed for synthetic materials.
4. How do I ensure the longevity of my prints?
Proper curing and using high-quality inks are crucial for ensuring the durability and longevity of your prints.
Read more related posts from Tobi Garment: